What
is Spring
Rate?
Spring rate refers
to the amount of weight needed to compress a spring
an inch (Example:500# per inch) To understand and properly check a spring
for rate you need to know the factors that determine the rate of the spring.
Fortunately, there are only three things that affect spring
rate, so there's not that much to remember!
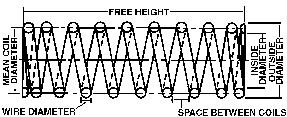
1. |
Wire
diameter. This affects rate since greater diameter wire is stronger
than lesser diameter wire. So, when wire diameter is increased, spring
rate increases. |
2. |
Mean
diameter of spring. Mean diameter is the overall outside diameter of
the spring less one wire diameter. When mean diameter increases, the
spring rate decreases. |
3. |
Active
coils. Determination of the number of active coils varies according to
spring design. Count the total coils minus two for springs with both
ends closed (includes all AFCOILS). Count the total coils minus one for
springs with one end closed and one end open. As the number of active
coils increases, the spring rate decreases. |
If a spring's
rate is linear (most racing springs
have linear rates) its rate is not affected by the load put onto the spring.
For example, a linear rate spring
rated at 500#/inch will compress 1" when a 500# weight is placed onto
the spring.
If another 500 pound weight is put onto the spring
the spring
will compress another inch. At this point the load on the spring
has increased to 1000 pounds. The rate of the spring,
however, remains constant at 500#/inch.
If the load put onto
a spring increases the rate of the spring, the spring is said to have
a progressive rate. Progressive
rate springs are sometimes used on
torque arms to absorb engine torque. Keep in mind that the load (or
preload) put onto a progressive rate spring can greatly increase the rate
of the spring.
Typically, progressive
rate springs
are made by varying the spacing between the springs'
active coils. During compression the close coils bottom out and deaden.
This reduces the amount of active coils and spring
rate increases as a result.
Springs that are
designed to include coils of different diameter or are wound using a tapered
wire will also produce a progressive rate.
Most coil springs
are actually progressive to some degree -- as we will learn later!
Dynamics
of Coil Springs:
There are basically
three different spring
designs presently used in race cars. They are:
TYPE I: |
Closed and ground on both ends (Coil-overs and rear conventional springs are this type). |
TYPE II: |
Closed both ends but ground one end only (Conventional front springs are normally this type). |
TYPE III: |
Closed and ground on one end and open on the other end (Similar to a conventional spring that has been cut). |
The 3 springs
types are used in different situations and provide different effects to
rate. Since the designs are so varied, it only follows that the dynamics
of each design are also varied (more later). You must remember, however,
the only factors that affect spring
rate are wire diameter, mean diameter, number of active coils.
How
Spring
Rates Change Dynamically:
Keep in mind that
as a coil spring
compresses, the inactive (dead) end coils gradually contact adjacent,
active coils. The contact causes the active coils to deaden which increases
the rate of the spring.
The rate creep that results usually stops after the first inch of spring
travel and does not appear again until spring
travel approaches coil bind. Generally speaking, this type of rate creep
is of little consequence with springs
softer than approximately 500#/inch. When you use springs
stiffer than 500#/inch rate creep becomes more pronounced.
It is important for
you to realize that springs
will pick up rate during compression. Consequently, the rate marked on
a spring
can differ from the rate as seen by the chassis. This is especially true
whenever a spring
manufacturer rates springs
based on the first inch of compression.
Example:
A racer replaced a 720# coil-over spring
with a 750# Afcoil. The racer believed he had stiffened his right front
spring,
however, the chassis behaved as though he had gone to a softer spring.
Upon rating both springs,
he found that the 720# spring
was rated for its first inch of travel (720# in.) and produced a much
higher (780# in.) rate for its second inch where it actually operated
on the race car. Because Afcoils are designed to give their nominal
rate closest to their actual working range of travel (this particular
750 spring
rated 735# in. for its first inch of travel and 755# in. for its second
inch), this racer actually softened up his race car even though the
spring
rate markings indicated the opposite! Rate creep can become even more
complex and more difficult to monitor for racers using conventional
type front coil springs
designed with an open end coil(type 3). The lower control arms used
with conventional springs
typically incorporate a stepped helix spring
seat built to an SAE specification (.720" of step). The helix seat was
designed into lower control arms to insure consistent installation of
the spring.
Keep in mind that any rotation of the spring
affects the actual installed rate of the spring.
Unless racing springs
used for this type of application are designed with one end coil that
closely matches the lower arm helix spring
seat, a serious amount of rate creep can result. To minimize this type
of rate creep, a conventional front spring
should be wound with its bottom end closed so that it sits squarely in
the helix seat. No active coil should touch the seat (just like the original
production spring
for which the control arm was designed -Type 2 spring).
When built in this
manner, a coil spring�s only contact with the lower control arm is through
an inactive (dead) coil (just like the spring's contact with the weight
jack). Consequently, as the spring compresses, the number of active coils
in the spring is not affected by the lower control arm. Therefore the
spring's rate remains constant throughout normal suspension travel. Some
rate creep still occurs due to contact between the dead end coils and
the adjacent active coils as was explained earlier, but the amount of
rate creep is miniscule compared to the rate creep produced by an open
end coil spring. All AFCOILS,
designed for use with stock lower control arms, are built in this manner.
If a spring
has an open end coil(type #3), the open end coil is active but gradually
deadens as the lower control arm moves against the spring.
A considerable increase in spring
rate occurs until the open end coil is completely seated in the helix.
For example, during
a test a 1500# open end coil spring
gained 464 lbs. of rate after 2 inches of spring
travel. By comparison, a 1300# Afcoil (closed end coil spring)
gained only 48 lbs. of rate after the same travel.
Further testing of
a series of open end coil springs
produced rate creep so inconsistent that at some points of spring
travel the springs
did not remain in the same rate order of softest to stiffest! It would
be very difficult to make predictable handling adjustments using springs
that exhibit such inconsistencies!
Keep in mind that
any load change to an open end coil spring
(via static weight, wedge, chassis roll, bumps, etc.) usually causes the
spring's
rate to change and, consequently, handling to change. If you are using
open end coil springs
you should chart their rates from static loaded height to fully loaded
height weight(in one inch increments). You should compare this information
before making spring
changes. By now you should realize the importance of using springs
that are designed to keep rate creep to a minimum.
What
is Spring
Stress?
As was pointed out
earlier, the rate of a spring
is determined by its diameter, the number of its active coils, and the
diameter of its wire. Since most racing springs
are built to a fixed diameter, a spring
designer must decide on the diameter of wire and the correct number of
active coils needed to produce the desired rate.
If the designer chooses
a smaller than normal diameter of wire (which tends to soften rate), he
will have to compensate by using fewer active coils (which tends to stiffen
rate) to achieve the desired rate. There are two possible reasons for
a spring
designer to use a smaller than normal wire diameter for a specific rate
spring:
1. |
The
ideal diameter wire may not be made and using the next larger wire
(which requires more active coils) would produce a spring with
insufficient spacing between its coils. This could cause the spring to
bind during normal operation. |
2. |
Cost
could be the prime consideration and by using a smaller diameter wire
and fewer coils (shortening the length of wire used) material cost is
reduced. Unfortunately, many racing springs are built this way and
these springs can cause a multitude of problems for the chassis tuner
that we will cover. |
Many racers mistakenly
believe extra spacing between the coils of a spring
indicates a preferable spring.
While a spring
must have sufficient stroke capacity it also must have sufficient material
to absorb the load put onto it. If the spring's
material is not sufficient for the load put onto the spring,
the material will become over-stressed and the spring
will take a set (lose height). Handling, of course, is affected and the
reason is not always apparent to the racer unless he pays close attention
to his springs.
Example: A typical
asphalt late model set-up calls for a tremendous amount of load on the
left rear spring
(upwards to 600 pounds more weight than on the right rear spring).
When the chassis sees normal spring
travel, the cumulative load on the left rear spring
produces a tremendous amount of stress in the spring.
If the spring
does not have sufficient material to handle the stress (as many don't),
it will take a set (as many do) and the car will lose crossweight and
tend to become loose off the corner. Excessive spacing between the coils
of a spring
is usually an indicator of a potential problem with spring
stress.
Stress
Consideration in Spring
Design
Many times, because
of the long stroke requirements for certain rates of racing springs,
material strength must be sacrificed to achieve significant stroke. Couple
this with the fact that the ideal wire diameter is not always made and
you can see why some springs
have a real potential to take a set. We have seen some brands of springs
lose as much as 15/16" of free height during normal operation. To eliminate
any set from occurring at the race track, it is good manufacturing policy
to pre-set (press to solid height) all racing springs
during their manufacture.
If done correctly,
pre-setting will generally eliminate any potential for additional set,
even when springs
are designed with smaller than ideal wire. Shot-peening will further enhance
a spring's
durability. It should be pointed out that all Afcoils are pre-set and
shot-peened during manufacture.
What
if a Spring
"Sets"?
When a spring
takes a set it will normally stabilize at its new height. The rate effectively
remains the same since no appreciable changes have been made to any of
the three factors that determine the spring's
rate. Other than creating a need to readjust the chassis (to restore the
original set-up and ride heights) the spring
should provide satisfactory performance. It is not uncommon for even well
designed and properly manufactured springs
to settle up to 1% of their free height. It needs to be pointed out, however,
that in cases where a poorly designed spring
is subject to extreme over-stressing, the spring's
height may not stabilize. The spring
may continue to change height (both shortening and lengthening) as the
spring
is worked. As a result, the set-up on the race car changes every time
the spring's
height changes. This can cause major chassis tuning headaches!
Monitor
your Springs:
We recommend that
you monitor the free heights of your springs on a regular basis. This
is so important that some Indycar teams measure their springs' heights
to the thousandth of an inch. Be sure to always measure height at the
same point on the end coils(mark your springs to indicate the measuring
point). You should suspect that a spring is setting whenever wheel weights
continually change. Under no circumstances should springs be used that
change more than 2% in height or do not stabilize in height. AFCOILS
are guaranteed to maintain their free heights to within 2% forever!
At the least you
should inspect all springs
for free height changes after racing on a very rough track or if your
race car was involved in a wreck. By now, you should realize there is
much more chance for a spring
to change its height than its rate. Consequently, you should spend your
time monitoring your springs'
free heights and not their rates!
What
is Coil Bind?
Coil bind occurs
whenever a spring
is compressed and one or more of the springs
active coils contacts another coil. The rate of the spring
increases whenever a coil binds since the bound coil or coils are no longer
active(this changes one of the three rate-determining factors). Of course,
handling is affected whenever a coil binds. If the spring
is compressed to solid height (all coils touching) during suspension movement,
the suspension will cease to work. You can, and should, check for evidence
of coil bind by examining the finish between the active coils. If any
coils have bound the finish between them will show contact marks that
appear as though they were drawn with a lead pencil. Normally any spring
that is binding should be replaced with a taller spring.
Be aware, however, there are racing springs
on the market that are built with wire that is heavier than what's needed.
These springs
will coil bind before others that are built with the proper size wire.
Under very extreme
conditions, coil binding can cause a spring
to unwind slightly. This can cause the mean diameter of the spring
to increase and reduce rate of the spring.
You should realize that the potential for coil bind is increased whenever
short springs
are used. Always match the spring
to the job.
Why
Springs
Bow:
Springs that have
lengths greater than 4 times their diameter will have a natural tendency
to bow when loaded. Consequently, tall springs
tend to bow more than short springs,
and small diameter springs
tend to bow more than large diameter springs.
Generally, the more a spring
is compressed the more it will tend to bow. Keep in mind the rate of a
spring
will increase if an active coil rubs another part of the race car. Here
are some tips to minimize bowing:
• |
Use
correctly fitting coil-over hardware or install weight jack assemblies
so that the spring mounting surfaces are kept as parallel as possible
during suspension travel.. |
• |
Use
springs that do not lean excessively (when positioned on a flat
surface). This indicates that the ends are ground parallel to each
other. This reduces the tendency for a spring to bow. You should check
both ends. |
• |
If
a coil-over spring is rubbing the shock, try reversing the spring so
the bowed part of the spring is around the shaft where there's more
clearance. |
• |
Use
coil-over springs that have straight sides rather than an hour glass
shape. This maximizes the clearance between the shock and spring. |
• |
Use springs that are wound straight. You can roll the spring on a flat surface to check for straightness. |
• |
The new AFCO XCS coil-over springs were developed specifically to eliminate bowing and shock hardware interference problems. |
There are special
manufacturing techniques that help to keep bow to a minimum. AFCOILS are
built for minimum bow under all racing conditions.
Spring
Checkers:
Unfortunately, we
know of no reasonably priced spring
checker that will accurately measure a spring
for rate. We have tested most brands of checkers and cannot give recommendation
to any. However, there are steps and procedures that can increase the
reliability of the spring
rate checkers commonly sold to racers. The accuracy of a spring
checker should be monitored. This can be done through the use of a checking
spring.
A checking spring
can be any spring
that has been accurately rated at one inch (or smaller) increments up
to a load close to the total capacity of the checker. It is important
that the free length of the checking spring
remain constant. The rates given by the checker can be compared to the
known rates of the checking spring
(at each increment of compression). Any rate discrepancies between the
checker and the checking spring
should be noted and taken into consideration when checking for rates of
other springs.
AFCO can provide
checking springs
for this purpose. The repeatability of a spring
rate checker should also be monitored. Simply put an old spring
in your checker and preload it to at least 20 lbs. Then compress the spring
and note gauge readings at 1" increments (or less) for the next three
or four inches of spring
travel. Tag the spring
with this information and use it occasionally to check for repeatability.
Make sure the free height of the spring
remains constant. Do not use the spring
if any change in free height occurs. A checking spring
can also be used to check for repeatability. A rate checker should consistently
repeat rates to within 2.5%.
Some Final Points on the use of Spring Rate Checkers:
• |
Preload Afcoil closed end conventional front springs 1/2". Coil-over and conventional rear springs should be preloaded 1". |
• |
Always
use similar preloads when checking different brands of springs. It's
best to preload springs to a height equal to their loaded height (as
installed in the race car) before checking for rate. This simulates
what the race car sees for spring rate. |
• |
Use a dial indicator to measure travel. |
• |
Take
dial indicator readings as close to the spring's center line as
possible. Readings taken very far from the springs center may not allow
for any rocking of the spring seat which distorts the actual amount of
spring travel. |
• |
Realize
travel indicated stiff springs can flex the framework and fixtures of
portable checkers. Consequently, the spring compresses less than its
indicated & the rate shows softer than actual. |
• |
The
dial indicator should hold steady whenever rate readings are being
taken. If the indicator moves, suspect the units framework is flexing
or there is a problem with the units jacking device. |
• |
Checkers equipped with load cells tend to be much more accurate than checkers equipped with hydraulic gauges. |
• |
Avoid checkers that allow the spring seats to rock in any manner or amount. |
• |
Always use the proper spring seats. |
• |
When using a helix type spring seat make sure the spring is positioned against the stop in the helix. |
We have pointed out
the more important features you need to consider when choosing and using
coil springs.
You should now have some basic understanding of the differences between
springs
and how those differences affect handling.
By knowing more about
springs
you will be able to confidently select springs
that suit your application and expect that they will give consistent and
trouble free performance.
|